MakMax Plus
What are the costs and estimated construction time for a new warehouse with “prefabricated construction”? Differences from other construction methods are also explained.
When looking to build a new warehouse cheaply and quickly, many people may first think of “prefabricated construction” as the old-fashioned “low-cost, short construction period” construction method that they often hear about.
This article describes the merits and cautions of building a new warehouse with prefabricated construction, as well as further options such as building a new warehouse with system construction.
Basic Information on "Prefabricated Architecture
What is prefabricated construction?
Prefabricated” is a Japanese abbreviation of the English word “prefabricated.
As the word “prefabricated” implies, prefabricated construction is a construction method in which components are made on the premise that they will be assembled in a predetermined procedure, and then assembled at the construction site according to the specifications and completed according to the predetermined specifications for each product, including dimensions. The construction is completed according to the pre-determined specifications for each product.
Various prefabricated buildings with different materials and detailed processes
There are various types of prefabricated buildings, depending on the type of materials and processes.
In terms of the different materials used, they can be broadly divided into heavy steel frame, light steel frame, and wood.
Depending on the process, there are mainly panel construction methods and unit construction methods.
Difference in materials: Heavy steel frame system
The construction period for heavy steel frame construction is relatively short because the main process is to bolt materials together at the construction site. Generally, they are constructed using a combination of the axial frame method (where vertical “columns,” horizontal “beams,” and diagonal “braces” are constructed from the foundation) and the panel method (where walls, roof, and other parts are produced and fabricated at a factory in advance and brought to the site).
The feature of this product is that it is resistant to fire, and its assembly process is less prone to deviations, which in turn allows for greater flexibility in floor plans.
The cost of heavy steel frames tends to be more stable than other components because the price of raw materials tends to be more stable during construction.
Difference in materials: Light steel frame system
Lightweight steel frames are constructed using lightweight steel frames. The lightweight steel frame is easy to handle and assemble on site, the construction period can be shortened easily and the quality is stable.
Differences in materials: wood-based
Wooden members may be used in prefabricated construction. Although the same as other materials in that the delivered components are assembled on site, wood-based components are easier to process in detail, making it easier to achieve the same degree of freedom in design and structure as wooden houses.
Difference in process: Panel construction method
The process of bringing panels for walls and floors to the site and assembling them.
Difference in process: Unit construction method
The entire box-shaped unit, including electrical wiring, water piping, and other facilities, is delivered to the site and installed as is.
Prefabricated buildings used for a variety of needs
Prefabricated construction is a construction method used for a wide variety of buildings, but it is particularly popular for warehouses, stores, offices, assembly halls, and large-scale facilities such as gymnasiums, commercial facilities, and factory facilities, where a uniform design and dimensions are not a problem, and the product is pre-determined. The construction method is often chosen when the design and dimensions of the product do not need to be predetermined.
Estimated construction time for prefabricated warehouse construction
When warehouses are built using prefabricated construction, the construction time required varies depending on the provider, the specifications of the prefabricated warehouse, and other factors, but here are some general guidelines for construction time.
- Heavy steel frame system, light steel frame system ……40 to 120 days
- Woody …… about 60 to 90 days
- Unit-based ……20 to 60 days
Although this is only a guideline, in most cases it takes about three months, and even less time is required for unit-type products, which are produced in boxes in advance and then assembled on site.
What is the cost of prefabricating a warehouse?
The cost of building a prefabricated warehouse includes the cost of the main components, foundation and exterior construction, and interior, exterior, and equipment costs.
As with the construction period, there are various differences in cost, depending on the business and the product.
- Prefabricated metal panel materials / Building area: 36 tsubo / Construction period: 120 days……1,200,000 yen approx.
- Prefabrication of lightweight steel frame and shaft panel materials / Building area: 90 tsubo / Construction period: 60 days……2,200,000 yen approx.
- Prefabricated metal panel materials / Building area: 56 tsubo / Construction period: 30 days……1,100,000 yen approx.
Advantages and disadvantages of building a warehouse with prefabricated construction (points to note)
As evidenced by the number of prefabricated warehouses that we actually see, prefabricated construction is one of the leading options for new or expanded warehouses.
Let’s review the advantages of building a warehouse with prefabricated construction and the disadvantages that should be kept in mind beforehand.
Advantage: Low-cost construction
Prefabricated buildings can be much less expensive to build than conventional construction methods.
However, as will be discussed in more detail below, there is also a simpler and lower-cost “tent warehouse” option for warehouse construction.
Advantage: Shorter construction period
Prefabricated buildings can be constructed in a short construction period because the components are made in advance to be assembled in a prescribed procedure.
Unit-based prefabricated construction will require an even shorter construction period, and even if not, prefabricated buildings will generally have a shorter construction period.
Advantage: A certain level of quality and accuracy can be expected because the parts and design are completed as a homogeneous building according to the specifications.
Unlike conventional construction methods, which are custom-made to order, the specifications for prefabricated buildings are all determined in advance at the component level, so the finished product will be consistent and in accordance with the specifications.
Since the product is completed as imagined at the time of preliminary inspection and selection of the product, it is unlikely that “it was not as expected after it was built” will occur in terms of quality and accuracy.
Advantage: Easily accommodates warehouse expansion or relocation
In addition to low cost and short construction time, prefabricated buildings of a certain shape and size make it easy to consider the compatibility with installation sites when adding more buildings.
Also, disassembly and reassembly are easier than with conventional construction methods, making it easier to relocate.
Disadvantages (points to note): Low degree of freedom in design and shape
The fact that the components used for assembly are prepared in advance is an advantage of the brace, which is completed simply by assembling it, but it also leads to a disadvantage of less flexibility in design and shape.
While there are, of course, several product types available from different companies, the shapes are generally general-purpose, square, and without decorative features or additional functions.
However, specifications and ordering methods for prefabricated building warehouses vary depending on the manufacturer and construction company providing the warehouse, so it is recommended that you check with the provider for details.
Disadvantages (points to note): Column spans (distance between columns to be installed) are shorter in many cases.
This is especially true in comparison with system architecture, which will be discussed later, but prefabricated buildings have more columns to support the structure, and may not be suitable for open interior spaces or warehouse spaces with a high degree of storage flexibility, for example.
Differences from "system architecture" and "tent warehouses," which are often mentioned in comparisons
In addition to prefabricated warehouses, there are other options such as “tent warehouses” and “system buildings” that can be used to build new warehouses at lower cost and in a shorter construction period.
The differences between them are briefly described below.
Each has its own advantages, so please refer to them as well.
Difference between prefabricated buildings and "tent warehouses
Tent warehouses, as the name suggests, are a simpler construction method than prefabricated warehouses, in which the roof and walls are constructed by covering them with membrane material.
It is characterized by even lower costs and shorter construction periods than prefabricated buildings.
Although generally inferior to prefabricated buildings in terms of durability, membrane walls and ceilings may be more appropriate for certain applications and are easier to replace in the event of an emergency.
There are also tent warehouses with enhanced durability itself.
Difference between prefabricated buildings and "system architecture
While prefabricated buildings are superior in terms of constant quality because their dimensions and components are predetermined, as mentioned above, there is little scope for choice in terms of design.
System construction is a construction method that builds on the advantages of the prefabricated construction method, but offers greater design flexibility and improved building quality than prefabrication.
In system architecture, advanced computer processing power is used from the design stage, and functional aspects such as heat insulation and sound insulation are enhanced through optimized and precise structural design.
▼ A list and comparison of the various construction methods for building warehouses is also detailed in this article. Please take a look at it as well.
Comparative explanation of construction method options for building a warehouse: conventional / prefabricated / system construction / tent
From tent warehouse leasing and rental to system construction warehouses, consult Taiyo Kogyo for your new warehouse construction needs!
Taiyo Kogyo offers “system construction” that adds flexibility and high quality to prefabricated construction methods, and “tent warehouses” that can be introduced at low cost.
Tent Warehouse offers both “rental” options, in which standard products are available for rent for a period of up to one year, and “lease” options, in which membrane structures can be used at a discount over a longer period of time, depending on your needs.
Customers who are considering prefabricated construction warehouses are encouraged to consider our products as a further option.
▼ Click here for product information on Taiyo Kogyo Co.
https://www.tentsouko.com/
When building a new warehouse, let's consider the purpose of the warehouse, such as "prefabrication," "tent," and "system construction.
When building a new warehouse, in addition to the “prefabricated construction” mainly introduced in this article, “system construction” and “tent warehouses” are also options, depending on the purpose and needs.
We urge you to consider the characteristics of each and select the most appropriate means.
Tent Warehouseへの
Any Inquries
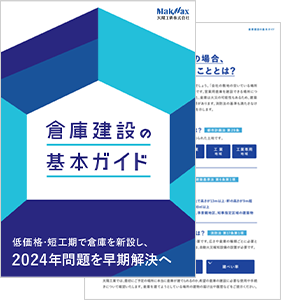
What you need to know when building a warehouse
We packed it all in.
Clues to solving the 2024 problem
Recommended for
I don't know where to start in building a warehouse.
I want to build a warehouse in an economical way.
Which type of warehouse should we build?
I want to learn the basics of warehouse construction anyway.
I'm concerned about the 2024 problem, but I don't know what to do about it.
Related Articles
- TOP>
- MakMax Plus>
- What are the costs and estimated construction time for a new warehouse with “prefabricated construction”? Differences from other construction methods are also explained.